FILAMENT FACTS
Discover key details about 3D printing filaments, our guide helps you choose the appropriate material for your particular application.
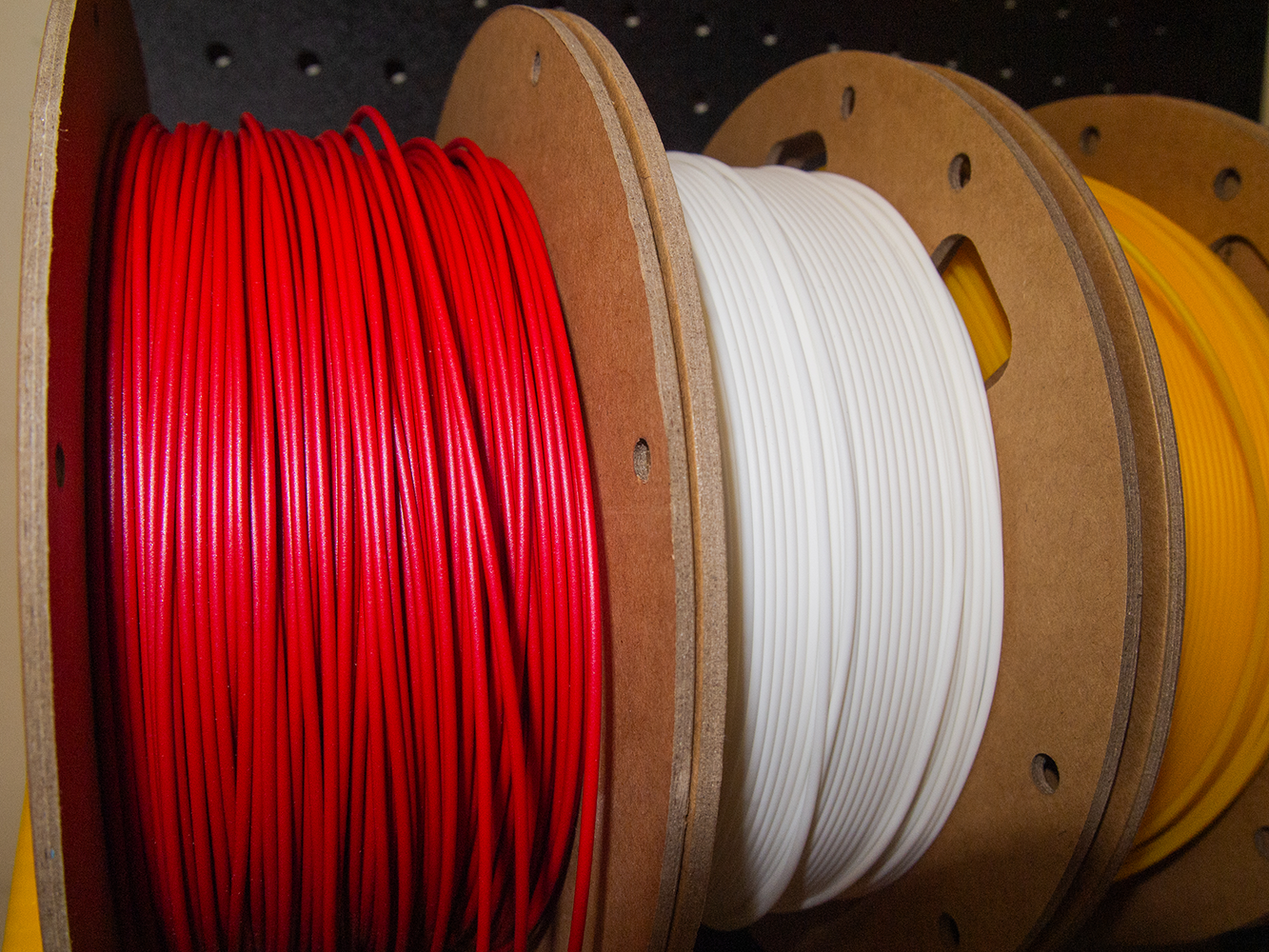
Foreword
Understanding 3D printing filaments and their associated properties is crucial for achieving a long-lasting, high-quality end-use part. Traditionally, 3D printing was primarily employed for rapid prototyping, aiding in fitment, stress testing, function assessment and various engineering evaluations. However, with the right filament selection, 3D printing has evolved beyond prototyping to serve as a viable end-use solution. Choosing the appropriate material ensures not only optimal performance but also the durability and reliability needed for functional parts in real-world applications.
Rule of Thumb
A general premises is that the more desirable the filament properties are means the harder it will be to print successfully. The ability to print engineering-grade filaments will be determined by the specifications of your particular printer, however, most "out-of-the-box" machines will be quite capable.
While the machine itself is critical in achieving high-quality results, without a knowledgeable user such outcomes may not be easily repeated. Understanding the necessary adjustments to each particular filament will not only enable consistent performance, but also save waste, time and the frustration involved with print failures.
Industrial-grade strength for demanding parts
Acrylonitrile Butadiene Styrene (ABS)
Known for its toughness and impact resistance, ABS is widely used in industrial applications. It’s lightweight and versatile, making it ideal for functional prototypes and end-use parts. However, ABS’s tendency to warp during printing means a heated bed or enclosure is essential. While great for 3D printing, injection moulding remains superior for large-scale ABS production.
Sustainable + vibrant + easy to print
Polylactic Acid (PLA)
PLA is a biodegradable plastic derived from renewable resources like cornstarch. In 3D printing, it’s favoured for its ease of use, low warping, and wide colour availability, making it ideal for prototyping and in-door aesthetic parts. It lacks high-temperature and impact resistance, limiting its use for functional applications. PLA’s biodegradability in industrial composting conditions also sets it apart from traditional plastics.
VERSATILITY + DURABILITY
Polyethylene Terephthalate Glycol (PETG)
PETG combines strength, flexibility and chemical resistance. Its durability and ease of printing make it a popular choice for functional parts, especially when transparency or food safety is required. PETG bridges the gap between rigid PLA and impact-resistant ABS, but its sensitivity to moisture and tendency to string can present challenges during printing.
Tougher + clearer
Polycyclohexylenedimethylene Terephthalate Glycol (PCTG)
PCTG is a variant of PETG with enhanced toughness and impact resistance. It’s an excellent alternative for applications requiring more flexibility than PETG. Its superior optical clarity and chemical resistance make it suitable for durable, high-performance parts, especially in consumer goods and industrial applications.
Flexibility + toughness for dynamic designs
Thermoplastic Polyurethane (TPU)
TPU is a flexible, rubber-like material with excellent abrasion resistance and elasticity. It’s used for producing functional parts like gaskets, seals and bushings. While TPU’s flexibility is its strength, it requires precise printer settings and slower speeds, making it less suitable for high-volume production compared to traditional methods like injection molding.
Built to withstand the great outdoors
Acrylonitrile Styrene Acrylate (ASA)
ASA offers high UV resistance and weatherability, making it ideal for outdoor applications. It’s similar to ABS but with improved colour stability and resistance to environmental stress. Its durability makes it suitable for automotive and construction parts, though printing ASA often requires a heated chamber to prevent warping and cracking.
high tensile strength + built for the heat
Polycarbonate (PC)
Polycarbonate boasts exceptional strength, toughness, and heat resistance - one of the strongest 3D printing materials. It’s commonly used for mechanical parts and enclosures requiring transparency and durability. However, PC’s high printing temperatures and sensitivity to moisture make it challenging to print without a high-end hotend setup as well as a filament drier.
Light + flexible + tough
Polypropylene (PP)
Polyprop is lightweight, flexible and resistant to fatigue and chemicals - ideal for living hinges, containers, and automotive parts. It is notoriously difficult to 3D print due to warping and adhesion issues, which often make traditional manufacturing methods more efficient. However, SLS 3D printing has enabled high quality, end-use results from Polypropylene.
Dissolves like magic for complex designs
Polyvinyl Alcohol (PVA)
PVA is a water-soluble material often used as a support filament for complex geometries. It’s highly effective in dual-extrusion setups where excessive overhangs would typically lead to poor layer adhesion resulting in terrible surface finishes. Its hygroscopic nature requires careful storage - it’s not suitable for standalone functional parts.
Dissolvable support or standalone strength
High Impact Polystyrene (HIPS)
HIPS is both a standalone material and a dissolvable support for ABS. As a primary material, it offers decent strength and machinability, making it suitable for lightweight parts. Its unique solubility in limonene allows for it to be used much like PVA as a support for complex geometry. HIPS’s brittleness compared to ABS limits its application in high-stress environments.
Recyclable strength with versatile applications
Polyethylene Terephthalate (PET)
PET is widely known for its use in plastic bottles, offering high strength, durability and recyclability. In 3D printing, it’s less common due to PETG’s superior ease of use, but it still finds application in scenarios requiring food-safe and tough materials.
Advanced blends for cutting-edge performance
Composites (CF, GF, etc.)
Composite filaments blend base plastics with reinforcing materials such as carbon fiber (CF) or glass fibers (CF). Carbon-filled composites offer exceptional stiffness and strength, ideal for lightweight structural components, while glass-filled composites enhance dimensional stability and impact resistance. While composites bring unparalleled mechanical properties, their abrasive nature requires hardened printer components and limits fine detail compared to pure plastics. These materials often outperform traditional manufacturing in small-batch or custom applications.